How Futura Trailers Aluminium Car Trailers Are Made | Manufacturing Materials & Techniques
At Futura Trailers we live by the values of Quality, Innovation, Simplicity, Reliability and Impressiveness.
Central to upholding these values are the materials and methods that we use in the construction of all of our aluminum car trailers - heat treated, anodized aluminum extrusion components that are bolted together, not welded.
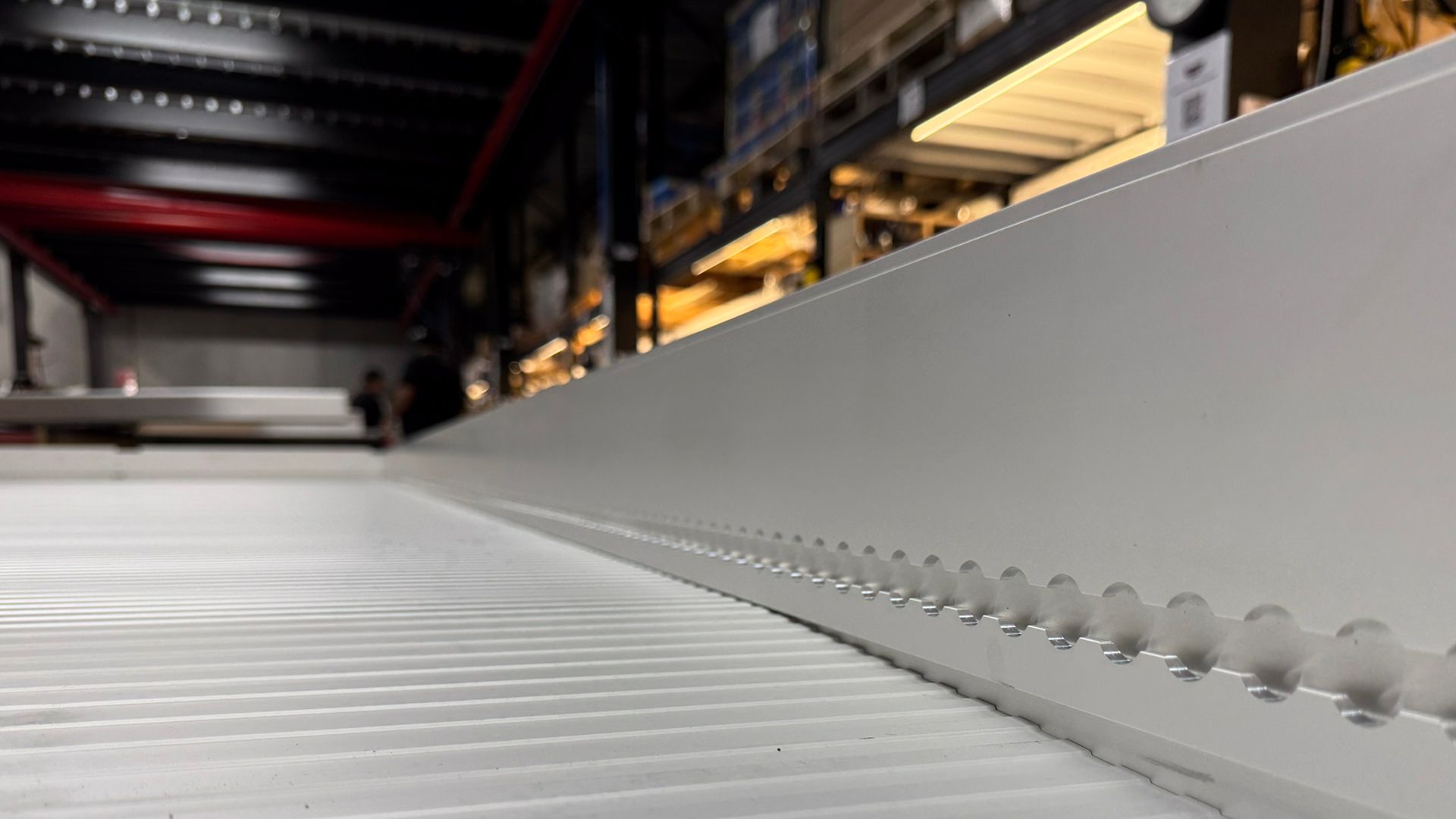
It is this approach to manufacturing that gives our aluminium car trailers and boat trailers the structural integrity, corrosion protection, ease of assembly and maintenance & good looks that are second to none.
Aluminium Alloy
Our aluminium extrusions are made with a marine-grade 6005-T6 aluminium alloy which is CNC machined to ensure accuracy before going through a heat treatment and anodising process.
Aluminium is one of the toughest materials on earth and is used in applications where high strength and durability are the most important considerations. It is used from planes to trains, buses to trucks – even some of the world’s tallest skyscrapers. Aluminium automakers are increasingly turning to aluminium as part of the multi-material mix to increase vehicle fuel efficiency while maintaining strength and safety.
The 6005-T6 aluminium alloy that we use contains a small amount of copper (<0.1%). The copper provides substantial increases in strength and facilitates precipitation hardening via heat treatment (see below).
Design & Engineering
At Futura Trailers we use Solidworks 3D engineering software to design all of our products. This provides the added benefit of FEA (Fine Element Analysis) engineering design capabilities. Futura’s design team goes through a rigorous design process ensuring each aluminium profile and the subsequent fabricated shape is designed, simulated and prototyped well before being put on the road.
Aluminium Extrusion
Extrusion is a widely used aluminum forming process that delivers almost unlimited possibilities in product design. The process of extruding aluminum begins with a solid, cylindrical block, or billet of metal. It is heated until softened and then forced through a steel die to produce lightweight, strong and corrosion-resistant components that are shaped like the opening of the die.
Aluminium extrusions are not only lightweight and recyclable, they have a higher strength to weight ratio relative to the steel or press-folded aluminium plate materials which have traditionally been used to manufacture trailers.
The benefit of extruded sections is that there is unlimited design flexibility in profile shape creation which allows the designer to put material only where it’s needed, reducing weight and adding strength where necessary.
The CNC Milling Process
A CNC (Computer Numerical Control) mill is a multi-axis cutting and forming machine that runs on a computer program. Multi-access CNC mills are excellent for prototyping as well as high-volume production. Aluminium has excellent machinability, and is thus the preferred material in most manufacturing sectors. CNC mills are also highly efficient allowing for more parts per billet of material with off-cuts collected for recycling.
Futura Trailers has several dedicated multi-axis CNC machines which ensure the accuracy and precision of fabrication meaning an unlimited number of trailer components can be produced repeatedly to exact standards to ensure the original design criteria and production demands are met.

Heat Treatment
Following fabrication, cutting, roll-forming and quality control Futura’s trailer components undergo a T6 two-phase heat treatment process to increase their fatigue performance and strength by as much as 30%.
Fatigue performance is a material or object’s ability to withstand destruction as a result of repeated loading and unloading cycles.
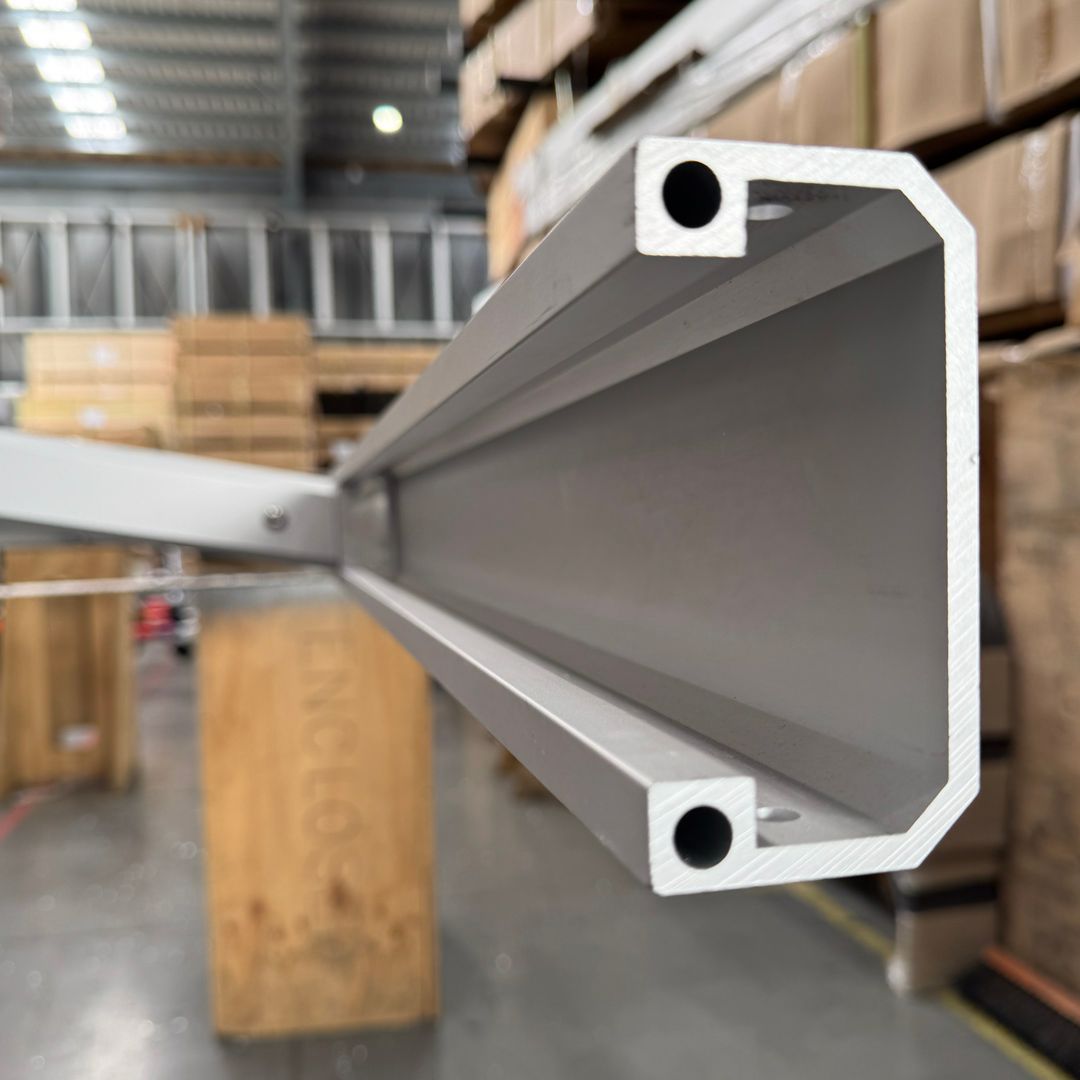
Phase One – Quenching
The alloy is heated to 500⁰C for 9-10 hours which causes the copper content to dissolve in the aluminium and form a single-phase alloy. This is achieved by cooling the alloy rapidly with water which supersaturates the aluminium with copper.
Phase Two – Ageing Phase
The alloy is heated to 180⁰C for 9-10 hours and then cooled by air allowing precipitation hardening. This forms copper aluminium crystalline structures, the size of which will dictate the strength. In general the smaller the crystals, the stronger the alloy becomes.
Heat treatment of folded aluminium trailer components, used in commonly fabricated aluminium car trailers & aluminium boat trailers, is generally not possible and therefore the shape and thickness of a folded aluminium trailer profile have to be increased to compensate for this.
Aluminium Anodising
Following the heat treatment process, each Futura part is placed in an electrically charged chemical bath which changes the molecular structure of the surface of the metal.
This anodising treatment creates a harder, more scratch-resistant surface and gives the base alloy an additional corrosion protection barrier. The Futura extrusion is anodised silver giving it a pristine finish that does not change colour and if kept clean and looked after will retain its ‘as-new’ appearance for decades.
Weld Free Assembly Process
Trailer chassis have traditionally been made by welding individual piece parts together. Welding is labor intensive and care must be taken to ensure that the welds fully penetrate the metal and are structurally sound.
Where the chassis is constructed with steel components, it is important to protect the steel and welds from corrosion. This is normally done by applying thick paint or galvanizing. Traditional trailer construction requires the skilled expertise of the welder to assemble and align the parts which can result in quality control issues.
Welding aluminum is a lot more technical and compounds these issues. Aluminum suffers an issue with weld fatigue – where welded aluminum components will crack around areas which have been welded. This is in part due to impurities within the metal which pool at the edges of the weld and create a weakened region, leading to fatigue cracking.
To address these issues Futura Trailers uses a patent pending aluminum connector to join its boat trailer chassis components together and high-quality fasteners for its car hauler trailers. Because the aluminum extrusions used by Futura Trailers don’t require any further cutting or shaping to create the connection points i.e. they are built-in already, a much smaller number of high-quality fasteners are used to assemble the chassis.
This allows Futura to produce a futuristic streamlined appearance without the need for welding or the use of numerous complex brackets and connection points. This provides a sleek, long-lasting anodised chassis which greatly reduces the corrosion and fatigue issues normally experienced with welded aluminum car trailers or steel car trailers.